Originally published February 10, 2023. Updated May 2, 2023.
Car 3618 was built by the Differential Steel Car Company of Findlay, Ohio, for use in track construction on the streetcar lines of the Boston Elevated Railway in Massachusetts. Its job was to carry ballast (crushed stone) to construction sites, and then spread the rock on top of the ties, so that it can be used to raise and level (tamp) the track. This hopper dump car is unusual because most electric railway companies used side dump cars (like our Pittsburgh Railways M551) for this job. In fact, fewer than ten cars of this type are known to have been built by Difco.
The car body of 3618 came to the Pennsylvania Trolley Museum in 1974 from the Seashore Trolley Museum in Kennebunkport, Maine. The car was subsequently refitted with wide gauge trucks from a former Pittsburgh work car and completely restored to operating condition.
The following is an update on the 2023 truck repair project from PTM’s trolley maintenance department manager, Bernie Orient:
As Car 3618 was not native to Pittsburgh, the original standard gauge trucks were not acquired and a surplus pair of Pittsburgh Railways work car trucks were modified to fit our broad gauge track. The wheels were quite worn and blamed for frequent derailments, so in 2007 we embarked on a mission to have the wheels “restored” by submerged arc welding. Because of time restraints we never got past the truck with the worst wheels, but we did acquire new springs, arch bars and brake levers for both trucks.
As presently we are at a lull with new track building (and thus 3618’s services will not be needed in the immediate future), I thought it was an opportune time to at least install the parts on hand into the second truck. It turned out to be most opportune as we lost two car spaces in the shop this winter to other pressing needs and had the manpower to spend on this project.
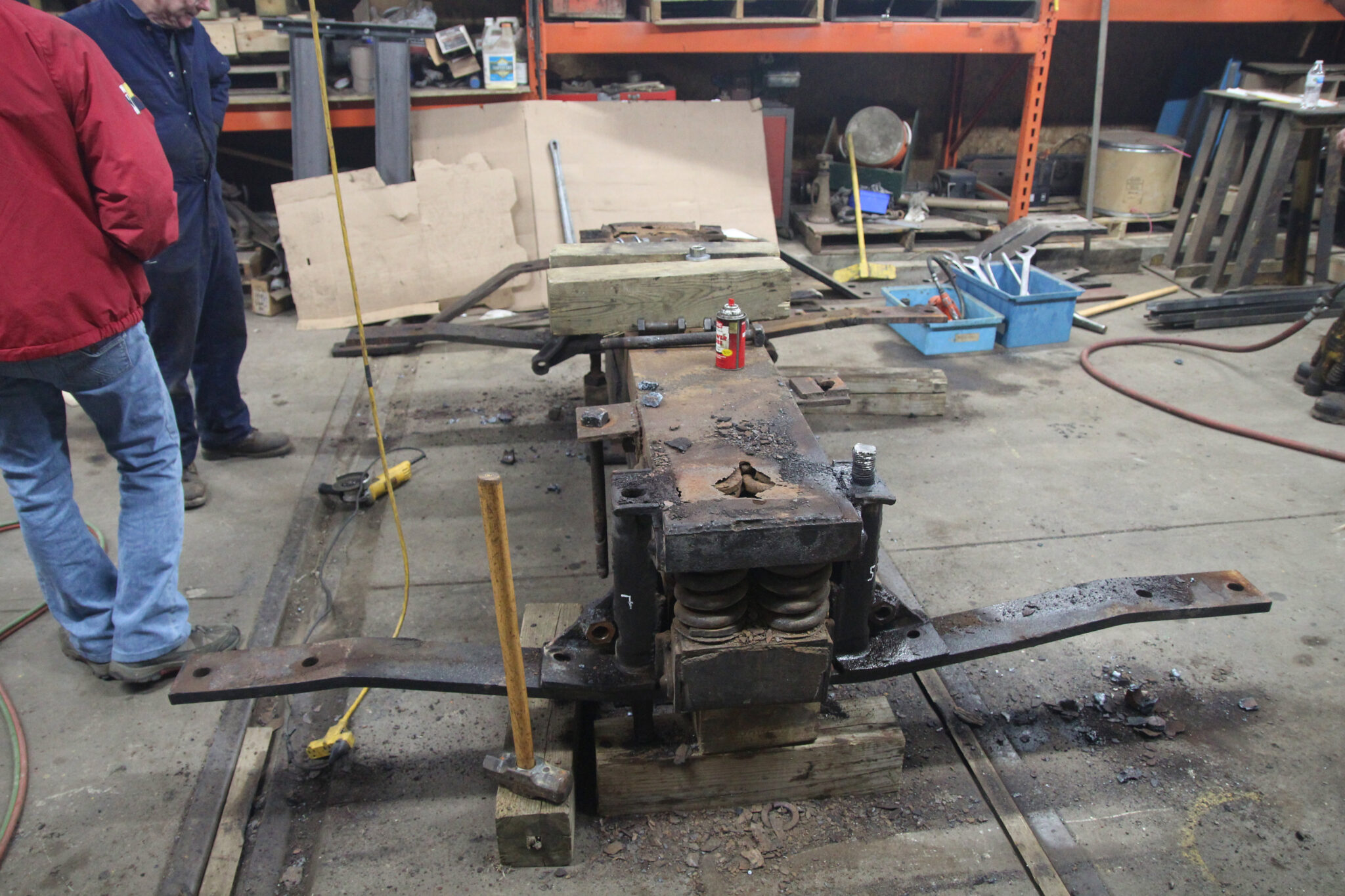
It did not take long for us to find the truck needed much more attention than parts replacement. The bolster — a steel fabrication that carries half of the car’s weight — was rusted through as shown in the above photo. It also had multiple cracks and twists. The bottom transom, not shown, is mainly a structural steel C-channel, and was likewise rusted through and bent. The reasons this was not observed during annual inspections is that the holes were obscured by the large arch-bars that span the wheelsets.
We also found three broken coil springs. The coil springs are located between the bolster and the bottom transom. Presently, Dan Bower and I are exploring the most economical way to produce these new assemblies. I might add that we posses the original drawings for the trucks drawn 99 years ago and know they were the original tucks beneath M283 crane car. There are undocumented stories of a nasty derailment with the crane car by its former owner wherein the trucks (or at least one) suffered significant damage. So we’re no doubt doing a belated clean-up now.
Update (April 2023): Over the following two weeks we got the truck taken apart and found the brake shoe holders and cast corner posts damaged and/or corroded beyond repair. By the end of March, we secured the transom, bolster and plasma-cut parts for the shoe holders, which were fabricated in-house. At this writing we are waiting on inner coil springs and the corner posts, both expected momentarily.